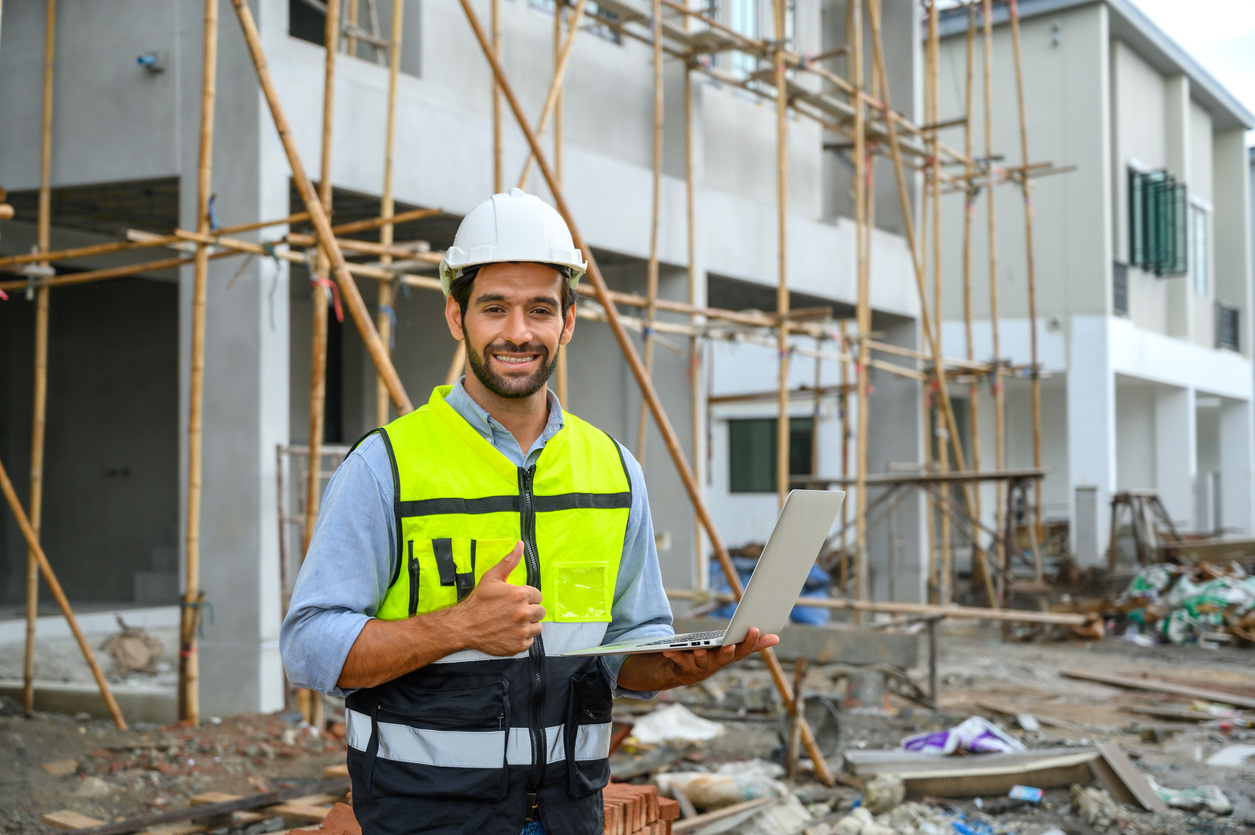
Using Bid Breakouts
Bid breakouts make reviewing an estimate relatively easy. When I bid a project I typically use three levels of breakouts. My first breakout is usually the base bid, alternates, value options or temporary power. My second is fixtures, switchgear, fire alarm, special systems, feeders, branch, devices, etc. This second list can become rather long, depending on the complexity of a project. My third level will generally be the drawing number. For large projects where a floor may have sectioned areas, I insert a fourth breakout between the systems and the drawing reference where I will insert the section area. The use of these breakouts will play a major role in the review of an estimate because they break a project into smaller, more manageable sections which are easier to understand and verify.Upon re-estimating the project I found that his estimate had missed the top four floors for all branches. This included all conduit, fitting, wire, labor, overhead and profit that should have been included in this project. Breaking out his bid would have shown this problem.
Several years ago, a contractor asked for a consultation. He had a new ten-story building, and during the bid process he had an excessive amount of conduit in his bid. He did not verify quantities or have his bid broken out even per floor. He turned out to be low bidder and was awarded the project. When I first reviewed it, the job was being completed on the eighth floor and the contractor had been out of conduit for some time. Upon re-estimating the project I found that his estimate had missed the top four floors for all branches. This included all conduit, fitting, wire, labor, overhead and profit that should have been included in this project. Breaking out his bid would have shown this problem.
Review Your Extension Sheet
When my bid is complete, I always print out my extension sheet from my estimating system. Once printed, I scroll down each sheet looking for correct materials, quantities that seem incorrect, correct material pricing, labor units and the ever-important multiplier that is used for all materials and labor units. I do this with a red pen and a 12” ruler and verify every sheet for accuracy on each bid. Once I have completed this check, I make corrections for every item needing repair. I then repeat the process to make sure that everything is correct. Remember, you only get one opportunity to be the low bidder, so you want to make sure your estimate is correct. If estimating manually, this process is just as important if not more so, as all items will be manually input and calculated, thus multiplying the odds of a mistake.
Use Electrical Estimating Software
If using electrical estimating software when completing your estimate, there are several items you should have preloaded into your system. I have used computer estimating programs for years, and all of these items are present on my system. However, I still keep a written copy of all of these items in a three ring binder. This is a throwback to the days when I estimated manually and reviewed this material while completing every estimate.
Have all of your labor rates (including burden) preloaded along with the overhead and profit levels that you expect to use. Any of these numbers can be adjusted quickly on the fly if a change is warranted.
Your typical non-productive labor, direct labor costs and any rental tool items regularly used should also be preloaded into your computer estimating system to act as a checklist to remind you of any possible expenses that may be required. Again, changes to these items for most electrical estimating software systems are typically adjusted at the last minute quickly.
My reviews begin before starting the estimate, when I set up the procedures used to estimate it in the first place. For me, this is working proactively and well worth the time and effort. When both the actual takeoff and entry into the estimating system are completed, it is a standard practice to review my efforts and make any changes needed.
Many contractors have wanted to know the secrets of my success, and this is one of them.